1、汽车涂装生产线厂房的空气洁净标准及要求
空气洁净度通常是指环境中空气含尘微粒量多少的程度。在单位计量体积下,含尘浓度高则洁净度低、含尘浓度低则洁净度高。空气洁净度的高低是用空气洁净度级别来区分的,而这种级别又是用操作时间内空气的计数含尘浓度来区分,也就是把某一个含尘浓度范围作为某一个空气洁净度级别。参考GB 50073—2013《洁净厂房设计规范》,洁净室按洁净度级别划分为1级、2级、3级、4级、5级、6级、7级、8级、9级,其中9级为最低级别。
根据涂装涂料试验验证表明:较小的颗粒(1.0μm≤粒径<5.0μm)对于漆面质量影响较小,但是同样需要避免较小的粉尘过多,因为较多的颗粒在一定条件下能够积聚形成大颗粒,所以对单位体积空气内的小体积颗粒数控制标准要求是<50 000个/(2.83 L)。5 μm≤粒径<10 μm的颗粒积聚成大颗粒的风险更为显著,所以控制标准:良好区间是<10个/(2.83 L)L,合格区间是<100个/(2.83 L)。粒径≥10μm的颗粒造成的污染漆面是目视可见缺陷,所以控制标准要求是<1个/(2.83 L)。因此,在汽车涂装生产线厂房环境中,需严格管控的微尘种类为3类:1μm≤粒径<5 μm,5 μm≤粒径<10 μm,10μm≤粒径。并以此定义汽车涂装生产线厂房的空气洁净标准及要求(见表2),而且厂房内的空气悬浮粒子浓度是受控的,确保洁净度可控。
参考GB 50073—2013《洁净厂房设计规范》,涂装洁净厂房空气的洁净度要求属于空气洁净度8级,汽车涂装生产线厂房内空气的颗粒浓度可以使用激光粒子计数器进行测量。该仪器的采样泵以2.83 L/min的速度吸入采样空气,同时对样本空气进行颗粒含量的测量。其测试流量为2.83 L/min),测试通道有6个,分别为0.3 μm、0.5 μm、1.0 μm、2.0 μm、5.0 μm、10.0 μm,可以分别测量各粒径范围的颗粒的浓度。根据测量结果,对照控制标准及要求,可以有效评价车间空气洁净度是否达标。
为了保证测量结果的可靠性,一般要求测量点在距离地坪高0.8 m的水平面内,测量点的分布要求覆盖车间主要工艺设备区域,尤其是车身物流路径区域,建议每个工艺层至少监控9个测量点,间距以20 m以上为宜。每个测量点测量3次,取其算术平均值,评价各测量点是否满足汽车涂装生产线厂房空气洁净度的控制要求。可以在车间工艺设备平面图上设置标注测量点,1周1次,从而有效评价车间空气洁净度。
2、汽车涂装生产线厂房送风洁净度规划
由于涂装车间具备良好的封闭性,车间内的空气交换主要通过厂房送风系统,因此厂房内空气洁净度的水平主要由厂房送风系统决定。而汽车涂装生产线厂房送风都是经过送风空调处理过后再送到厂房内部的。故为了确保空调送风的洁净度,需要对送风空调系统的功能段布置及配置做好规划设计。
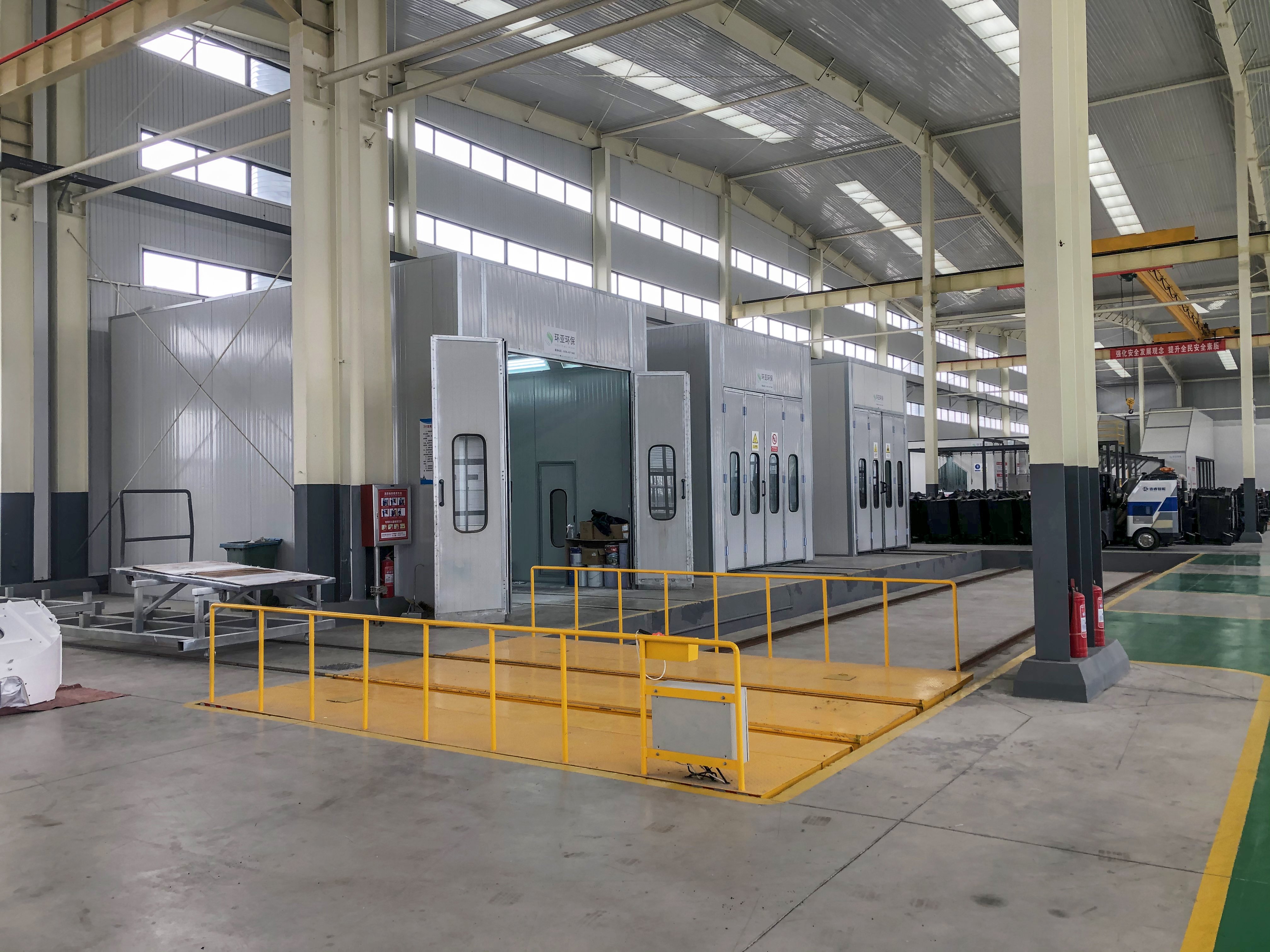
汽车涂装生产线厂房送风空调的温湿度控制要求不同于工艺送风空调的恒温恒湿,它一般要求恒温控制,湿度范围控制。这样既保证了车间内部环境温度,也通过控制湿度的范围来提高车间内部的清洁度,并且有效降低能源消耗。根据功能需求,厂房送风空调一般设置为以下8个功能段:G3过滤段、燃烧器段、F5过滤段、冷盘管段、热盘管段、风机段、F7过滤段、消音器段。加湿段的设置依据各地气候条件进行增减(相对湿度控制范围40%~70%)。
各个功能段的作用为:燃烧器段主要是采用天然气直燃的方式给空气加热,提高送风温度,主要用于冬季,采用天然气直燃的加热方式相对于蒸气加热更节能。冷热盘管段的作用主要是在夏季改变空气的温湿度,当需要降低空气温度并改变湿度时,通常先冷盘管降温后再热盘管升温调节。风机段主要是安装送风风机及电机,将已处理过的空气送入待用区域。消音段主要是安装消音器,降低送风噪音,确保车间内部噪音低于85 dB的法规要求。
3、个过滤段的最末一级设置的过滤器等级决定了送风空调送出去的空气的净化程度。而上级各级过滤器起保护作用,它们保护下风段过滤器以延长其使用寿命,同时保护空调其他功能段的正常工作。在空调设计规划中,应该首先根据汽车涂装生产线厂房洁净度的要求确定最末一级过滤器的等级,然后选择起保护作用的过滤器。
汽车涂装生产线厂房送风空调的3道过滤器规划设计的目的是:G3过滤段设置在燃烧器段前,主要是为了起到提高燃烧器段的洁净度,避免燃烧头的堵塞。F5过滤段设置在冷热盘管及风机段前,主要是利用F5过滤效果确保后续功能段的清洁,避免因为污染而增加清洁维护的难度。F7过滤段设置在风机段后,主要考虑前面几个工艺段在做维护的过程存在外来污染风险,F7过滤能起到最后屏障作用,保障送往汽车涂装生产线厂房内部的空气洁净度。
4、厂房送风空调过滤等级的设置
涂装洁净厂房空气的颗粒浓度要求属于空气洁净度8级,要求空气中粒径≥10 μm的颗粒数为0,5 μm≤粒径<10 μm 的颗粒数为100以下。所以空气经过送风空调处理后需要捕捉空气里所有粒径≥5 μm的颗粒。对比过滤器等级标准可知,厂房送风空调的最末一道过滤等级应该为F7(所有粒径≥5 μm的颗粒捕捉效率约为100%)。
而前面两道预过滤的过滤等级配置,主要考虑其颗粒捕捉效率,既能有效防护相应功能段的清洁度,又能延长F7过滤器的使用寿命。所以依据隔级配置保护的原则分别别配置了G3和F5的过滤器。由于其他工艺空调的送风也会溢流到厂房内,所以其他工艺送风的最末一道过滤器的过滤等级应该不得低于F7。
不过,选择过滤器还要全面考虑洁净室的特性、过滤器特性和净化系统特性。要保证送风洁净度,仅有合格的过滤器是不够的,要保证运输、安装过程中不损坏过滤器及安装的正确,还要做好过滤器使用过程的中的压差监控。
5、涂装洁净厂房微正压控制
参考GB 50073—2013《洁净厂房设计规范》要求:洁净区与室外的压差应该不低于10 Pa。试验研究的结果表明,洁净室内正压值受室外风速的影响,如果要保证室内的清洁度,室内正压值必须高于室外风速产生的风压力。当室外风速大于3 m/s时,产生的风压力接近5 Pa,若洁净室内正压值为5 Pa时,室外的污染空气就有可能渗漏到室内。但根据现行国家标准《采暖通风和空气调节设计规范》GB 50019编制组提供的全国气象资料统计,全国203个城市中有74个城市的冬夏平均风速大于3 m/s,占总数的36.4%。这样如果洁净室与室外相邻时,其最小的正压值应该大于5 Pa。因此,规定洁净室与室外的最小压差为10 Pa。
为了防止汽车涂装生产线厂房内的空气洁净度受到外界空气的污染,所以应该确保厂房对室外呈微正压状态,控制标准为汽车涂装生产线厂房与室外的最小压差为10 Pa,该压差为绝对压差。
由于厂房内部相对于室外的压差是由于厂房内的送风量大于排风量而产生的,所以要想控制好汽车涂装生产线厂房的微正压状态。需要控制送排风量的相对状态。要想达到该微正压控制要求,在规划设计时,首先是根据压差要求,选定厂房内换气次数的标准。参考行业设计经验,结合汽车涂装生产线厂房的密封效果,汽车涂装生产线厂房的换气次数要求为≥1.2次/h。而这个换气次数,是用来核算厂房送风空调送风量需求的主要依据。
由于厂房内相对于室外的压差取决于厂房的送风量与排风量之差,因此若要使厂房相对室外的压差保持稳定状态,首先应该令送风与排风量保持一定。实现此要求的具体做法较多,如在总送风管上安装微差压传感器,当风量发生变化时,即可通过变频器改变送风风机转速,从而使总送风量保持不变;同样,在总排风管上也可安装微差压传感器,当风量发生变化时,即可通过变频器改变排风风机转速,使总排风量保持不变。以此达到送排风量差的稳定。
在一定的压差要求下,厂房的换气次数与厂房的密封性有关,厂房的密封性效果越好厂房的换气次数要求越少。而且由于密封性效果好,厂房微正压受到外界的干扰低,稳定性也高。
此外,由于厂房内的新风都是由室外新风通过送风空调处理后送进车间的,所以换风次数的增多会使得送风空调的送风量增大,从而导致能耗增大,不利于车间节能的要求。
因此规划设计具有良好密封性的汽车涂装生产线厂房,对保障汽车涂装生产线厂房的微正压状态及洁净度控制很有必要。由上述的分析可以知道,影响厂房密封性较大的风险点有3个,分别是本车间与焊装车间相连接的通道开口、本车间与总装车间相连接的通道开口、车间物料进入的物流门。
所谓的风压就是垂直于气流方向的平面所受到的风的压力。根据伯努利方程得出的风-压关系,风的动压:p=0.5ρv²:
(1)其中 p 为风压,kN/m², ρ 为空气密度,kg/m³, v 为风速,m/s。由于空气密度 ρ 和重度 r 的关系为 r = ρg , 因此有 ρ = r / g 。在式(1)中使用这一关系,得到p=0.5 rv ²/ g
(2)此式为标准风压公式。在标准状态下(气压为101.325 kPa., 温度为15 ℃), 空气重度 r =0.012 25 kN/m³。纬度为45°处的重力加速度 g =9.8[m/s²], 我们得到 p = v ²/1 600。所以要想得到洁净厂房对室外的绝对压差为10 Pa,如果对室外有开口的地方,平均溢流风速为4 m/s。
这3个风险点总开口面积约为30 m²,如果不能有效控制,将会导致432 000 m³/h的空气泄露。因此在规划阶段要重点考虑如何优化这几个风险点。
与总装及焊装的通道开口,可以采取安装快速卷帘门的方式来减少空气溢流量,当车身或滑撬通过时打开,通过后快速关闭。车间物料进入的物流门,设置双道卷帘门,物料进入时采用一个开启另一个关闭防止外界颗粒的进入,而且在最外侧的卷门内安装风幕,有效防止外界污染。
人员进入车间的通道,可以设置风淋室室或双道带闭门器的门。其他门正常运行的时候都是常闭状态,严禁无故开启。
以上措施的实施,大大减少了厂房空气泄漏量,降低厂房换风次数的需求,降低了车间运行费用,也为厂房实现微正压稳定状态提供了保障。
厂房风平衡调试完成后,定期检查现场的压差装置及显示数据,监控厂房微正压状态。随时了解现场发生的状况,并及时提醒操作人员注意压差的稳定保持。
汽车涂装生产线厂房空气洁净度控制的规划设计,需要从洁净度标准的定义,到送风洁净度的总体规划,再到厂房的微正压控制规划3个方面着手去分析。并根据分析去落实各项要求,为汽车涂装生产线厂房内空气洁净度达标提供有力的支撑。汽车涂装生产线厂房空气洁净度的管理除了在规划阶段注重设计方案的科学合理性,还需要在车间投产运行期间做好相应的维护管理,比如定期良好的深度清洁,日常进厂物料的清洁控制,最为关键的是日常的维护清洁。上述方法总体的方向是减少外来污染,同时加快内部污染的自净速度。这样可以有效改善汽车涂装生产线厂房内的空气洁净度,提升生产线上的产品质量水平,并逐步降低车间的运营费用。
版权声明:本网注明来源为“乐发环保”的文字、图片内容,版权均属本站所有,如若转载,请注明本文出处:http://www.keketie.com 。同时本网转载内容仅为传播资讯,不代表本网观点。如涉及作品内容、版权和其它问题,请与本网站联系,我们将在及时删除内容。