背景与意义
近年来,化工工业进入了快速发展阶段,企业在加大新技术应用和新产品开发力度的同时,也始终注重经济效益和环境效益的统一,同时国家也越来越注重工业废气的排放标准。由石油化工、轻工、印刷行业以及机动车发动机排出的挥发性有机化合物(Volatile organic compounds,简称VOCs)废气,已成为大气中的重要污染源之一。PTA氧化反应尾气是PTA装置排出的数量*大的有害气体,其中主要的污染物为乙酸甲酯、对二甲苯和溴代烃类,其中乙酸甲酯高达14600mgm3,对二甲苯达2420mgm3,总溴达228mgm3,其中以乙酸甲酯的含量*高,而且酯类被认为是一类较难脱除的VOCs。PTA氧化尾气中
VOCs(挥发性有机化合物)含量为中、低浓度,若采用回收技术法,存在处理效率低、装置体积大、成本高等缺点。降解技术中目前较为成熟的是直接燃烧和催化燃烧技术。直接燃烧是通过800~900 ℃高温直接氧化尾气中的有害物质为CO2和水,脱除效率可超过99%,但直接燃烧成本价高;催化燃烧是借助于催化剂的作用,使有害物质的分解温度降低到280~450 ℃,催化燃烧法具起燃温度较低、氧化温度低、能耗低、效率高,NOx生成量极少,无二次污染物等优点。在自动控制领域中,控制的要求总是在不断提高,在尾气处理的中合适地选择控制策略和选用仪表可以很好地改善系统的稳定性和可控性,节省资金投入,促进控制系统的普及,取得整体经济的发展和较好的环保效益。
但由于催化燃烧过程会有大量易燃易爆化学气体,且往往采用高温高压操作方式,因此实验室很难建立实验装置展开相关的工程应用研究。与此同时,以信息技术、相似原理、系统技术及其应用领域有关的专业技术
为基础,以各种物理效应设备和计算机为工具,借助系统模型对实际的或设想的系统进行试验研究,展开工业精馏过程流程模拟与集成监控方法的应用研究具有很高的工程实用价值。虽然仿真代替不了实际中的生产情况,但可以模拟、验证该方案的可行性。所以近年来,化工过程的计算机仿真监控平台的设计和故障诊断等方面得到了迅速发展。
1.2催化燃烧基本原理
催化燃烧是借助催化剂在低温下(200~400℃)下,实现对有机物的完全氧化,因此,能耗少,操作简便,安全,净化效率高,在有机废气特别是回收价值不大的有机废气净化方面,比如化工,喷漆、绝缘材料、漆包线、涂料生产等行业应用较广,已有不少定型设备可供选用。
1)催化剂定义:催化剂是一种能提高化学反应速率,控制反应方向,在反应前后本身的化学性质不发生改变的物质。
2)催化作用机理:在一个化学反应过程中,催化剂的加入并不能改变原有的化学平衡,所改变的仅是化学反应的速度,而在反应前后,催化剂本身的性质并不发生变化。而实际上,催化剂本身参加了反应,正是由于它的参加,使反应改变了原有的途径,使反应的活化能降低,从而加速了反应速度。例如反应A+B→C是通过中间活性结合物(AB)过渡而成的,即:A+B→[AB]→C,其反应速度较慢。当加入催化剂K后,反应从一条很容易进行的途径实现:A+B+2K→[AK]+[BK]→[CK]+K→C+2K,中间不再需要[AB]向C的过渡,从而加快了反应速度,而催化剂并未改变性质。
3)催化燃烧的工艺组成:不同的排放场合和不同的废气,有不同的工艺流程。但不论采取哪种工艺流程,都由如下工艺单元组成。
1.废气预处理: 为了避免催化剂床层的堵塞和催化剂中毒,废气在进入床层之前必须进行预处理,以除去废气中的粉尘、液滴及催化剂的毒物。
2.预热装置: 预热装置包括废气预热装置和催化剂燃烧器预热装置。因为催化剂都有一个催化活性温度,对催化燃烧来说催化剂是起燃温度,必须使废气和床层的温度达到起燃温度才能进行催化燃烧,因此,必须设置预热装置。但对于排出的废气本身温度就较高的场合,如漆包线、绝缘材料、烤漆等烘干排气,温度可达300℃以上,则不必设置预热装置。预热装置加热后的热气可采用换热器和床层内布管的方式。预热器的热源可采用烟道气或电加热,目前采用电加热较多。当催化反应开始后,可尽量以回收的反应热来预热废气。在反应热较大的场合,还应设置废热回收装置,以节约能源。预热废气的热源温度一般都超过催化剂的活性温度。为保护催化剂,加热装置应与催化燃烧装置保持一定距离,这样还能使废气温度分布均匀。
1.3化学反应器的基本控制策略
影响化学反应的扰动主要来自外部,因此控制外围是反应器控制的基本控制策略。稳定外围控制是尽可能使进入反应器的每个过程变量保持在规定数值的控制,它使反应器操作在所需操作条件,产品质量满足工艺要求。通常,稳定外围的控制一句物料平衡和能量平衡进行,采用的基本控制方法如下:
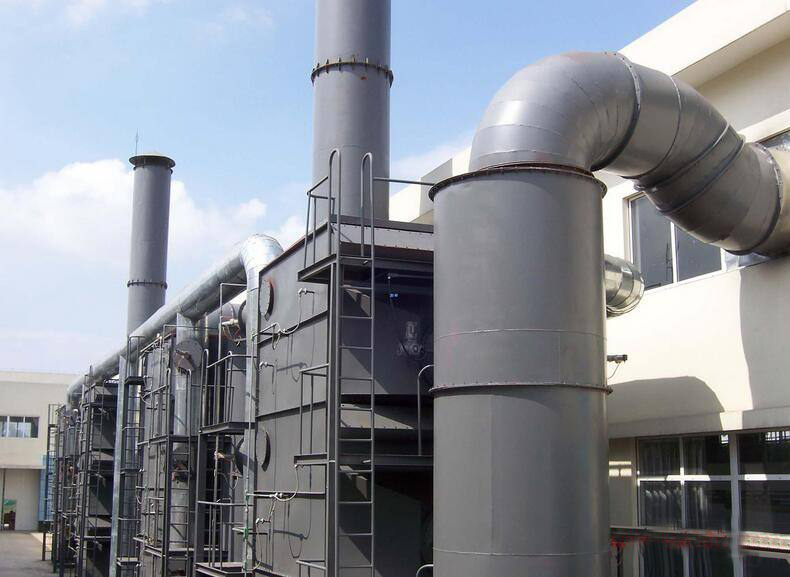
1)反应物流量的控制
为保证进入反应器物料的恒定,可采用参加反应物料的定值控制,同时,控制生成物流量,使由反应物带入反应器的热量和由生成物带走的热量也能够平衡。反应转化率较低,反应热较小的绝热反应器或反应温度较高,反应放热较大的反应器,采用这种控制策略有利于控制反应的平稳进行。
2)流量的比值控制
多个反应物料之间的配比恒定是保证反应向正方向进行所必需的,因此,不仅要静态保持相应的比值关系,还需要在动态时保证相应的比值关系,有时,需要根据反应的转化率或温度等指标及时调整相应的比值。为此,可采用单闭环,双闭环比值控制,有时,可采用变比值控制系统。
3)反应器冷却剂量或加热剂量的控制
当反应物量稳定后,由反应物带入反应器的热量就基本恒定,如果能够控制放热反应器的冷却剂量或吸热反应器的加热剂量,就能够使反应过程的热量平衡,使副反应减少,及时地移热或加热,有利于反映向正方向进行,因此,可采用对冷却剂量或加热剂量进行定值控制或将反应物量作为前馈信号组成前馈-反馈控制系统。
4)化学反应器的质量指标是*主要的控制目标
对反应器的控制,主要被控变量是反应的转化率或反应生成物的浓度等直接质量指标,当直接质量指标较难获得时,可采用间接质量指标。例如,温度或带压力补偿的温度等作为间接质量指标,操纵变量可以采用进料量,冷却剂量或加热剂量,也可以采用进料温度等进行外围控制[1]。
1.4控制系统仿真软件的应用研究现状
近十年来,随着MATLAB语言和Simulink仿真环境在控制系统研究与教学中日益广泛的应用,在系统仿真、自动控制等领域,国外很多高校在教学与研究中都将MATLABSimulink语言作为首选的计算机工具。我国的科学工作者和教育工作者也逐渐认识到MATLAB语言的重要性,并且在很多高校的本科自动控制原理实验教学中得到应用[2,3,4]。
在自动控制领域里的科学研究和工程应用中有大量繁琐的计算与仿真曲线绘制任务,给控制系统的分析和设计带来了巨大的工作量,为了解决海量计算的问题,各种控制系统设计与仿真的软件层出不穷,技术人员凭
借这些产品强大的计算和绘 图功能,使系统分析和设计的效率得以大大提高。然而在众多控制系统设计与仿真软件中,MATLAB以其强大的计算功能、丰富方便的图形功能、模块化的计算方法,以及动态系统仿真工具Simulink,脱颖而出成为控制系统设计和仿真领域中的佼佼者,同时也成为了当今*流行的科学工程语言[5,6]。
MATLAB是MathWorks公司于1982年推出的一套高性能的数值计算和可视化软件。它集数值分析、矩阵运算、信号处理和图形显示于一体,构成了一个方便、界面友好的用户环境。它还包括了ToolBox(工具箱)的各类问题的求解工具,可用来求解特定学科的问题。MATLAB所具备的强有力的计算功能和图形表现,以及各种工具箱提供的丰富的专用函数,为设计研究人员避免重复繁琐的计算和编程,更快、更好、更准确地进行控制系统分析和设计提供了极大的帮助。 MathWorks公司于2011年4月发布了MATLAB的*新版本——2011a(R2011a) 版MATLAB和Simulink产品系列。该版本的核心在于引入了新一代的代码生成产品:MATLAB Coder、Simulink Coder和Embedded Coder。
1.5仿真模型与监控平台间的通讯技术
根据现有资料,Matlab和监控组态软件之间的数据交换方法有很多种,其中以动态数据交换DDE为主,动态数据交换是Windows系统中支持进程间的通信机制,它是以共享内存来实现数据交换的。大量的文献表明了采用DDE数据交换技术实现组态软件和MALAB的数据通信的有效性。但DDE存在的缺陷是:当通讯数据大时,数据刷新速度慢,容易出现死机现象;DDE本身的窄带宽,并不非常适用于实时交换系统,而这种实时系统却为自动化控制所必需。OPC以其独有的开放性、互连性、高效性和产业性占据了主导地位。OPC是OLE for Process的缩写,即把OLE应用于工业控制领域,采用客户服务器体系。
在工业过程的实际应用中,大多数监控组态软件都拥有开发商自主开发的专有实时数据库和历史数据库。如果要访问这些数据库,以前必须要编写相应的代码程序调用开发商提供的API函数或其他特殊方式来实现。随着OPC技术的广泛应用,国内流行的监控组态软件,如RSVIEW32、Ifix、WinCC、MCGS、Kingview 等全面支持OPC技术,即这些组态软件提供了可以访问数据库的OPC服务器,任一客户端无需了解接口特性,只要按照OPC规范编写客户端服务程序即可读取和写入监控组态软件实时数据库中的数据。
1.6化工过程集成监控软件
组态软件的应用领域很广,它可以用于电力系统、给水系统、石油、化工等数据采集与监视控制以及过程控制等诸多领域。随着工业自动化水平的提高,以及计算机技术的广泛应用,人们对工业监控软件的通用性和灵活性提出了更高的要求。组态软件(configuration software)是指一些数据采集与过程控制的专用软件。它们是在自动控制系统监控层一级的软件平台和开发环境,能以灵活多样的组态方式提供良好的用户开发界面和简洁的使用方法,其设置的各种软件模块可以非常容易的实现和完成监控层的各项功能,为自动化工程技术人员提供了一种设计控制策略及控制界面的工具。
WinCC(windows control center)是由德国西门子公司与微软公司共同开发的软件系统,是结合西门子在过程自动化领域中的先进技术和计算机软件强大功能的产物。WinCC是一个功能强大、接口丰富的监控系统,既可以用来完成小规模、简单的过程监控应用,也可以用来完成复杂的应用。WinCC将Windows NT应用程序的现代体系结构与使用方便的图形设计程序结合在一起,可以很方便地生成人机界面,建立完整的过程监控解决方 案。
WinCC监控平台设计软件有着通用的应用程序,适合所有工业领域的解决方案;拥有多语言支持,全球通用 ;它可以集成到所有自动化解决方案内,内置所有操作和管理功能,可简单、有效地进行组态,可基于Web持续延展,采用开放性标准,集成简便;而且它集成的Historian 系统可以作为IT 和商务集成的平台,可用选件和附加件进行扩展,适用于所有工业和技术领域的解决方案。
WinCC监控平台设计软件集生产自动化和过程自动化于一体,实现了相互之间的整合,这在大量应用和各种工业领域的应用实例中业已证明,包括:汽车工业、化工和制药行业、印刷行业、能源供应和分配、贸易和服务行业、塑料和橡胶行业、机械和设备成套工程、金属加工业、食品、饮料和烟草行业、造纸和纸品加工、钢铁行业、运输行业、水处理和污水净化。
WinCC提供了所有*重要的通讯通道,用于连接到SIMATIC S5S7505控制器(例如通过S7协议集)的通讯,以及如PROFIBUS-DP FMS、DDE(动态数据交换)和OPC,(用于过程控制的OLE)等非专用通道;亦能以附加件的形式获得其它通讯通道。
WinCC在其基本系统内集成了基于Microsoft SQL Server 2000的功能强大、可延展的“Historian”系统,并以跨公司“Historian”服务器的形式用作中央信息交换系统。不同的评估用客户机、开放性接口(开放性数据库接口:ADO,OLEDB,SQL;编程接口:VBScript和有访问COM对象模型和API功能的ANS I - C)以及各种任选件(WinCCDat @Monitor,
WinCCConnectivity Pack,WinCC, Industrial Data Bridge)构成了灵活而高效的集成监控平台的基础,这样就可以与生产和公司管理层软件(MES和ERP)相连接。
版权声明:本网注明来源为“乐发环保”的文字、图片内容,版权均属本站所有,如若转载,请注明本文出处:http://www.keketie.com 。同时本网转载内容仅为传播资讯,不代表本网观点。如涉及作品内容、版权和其它问题,请与本网站联系,我们将在及时删除内容。