循环流化床干法烟气脱硫脱硝除尘一体化技术是近几年国际上新兴的烟气治理技术,具有脱硫脱硝除尘效率高、无污水排放、产物易于处理的优点,同时投资相对较低,设备可靠性高,运行费用较低,因此倍受社会关注。本文结合企业实际较为详细的介绍该工艺装置运行中存在的问题、解决办法和节能降耗工艺优化方案。
新疆某公司根据环保需要,新建干法脱硫脱硝除尘一体化装置,属于全新工艺,存在很多问题,运行成本也较高,需对装置进行优化运行研,以实现节约成本,降低消耗,达标排放目的。
1 烟气脱硫脱硝除尘工艺和现状
目前该公司3×220t/h煤粉锅炉烟气脱硫采用的是干法循环流化床脱硫技术,脱硫剂为电石渣;脱硝工艺分为两级,炉内采用低氮燃烧+SNCR工艺,炉内脱硝后的烟气进入干法脱硫脱硝除尘一体化设施,再进行COA脱硝,COA脱硝以亚氯酸钠为氧化剂,将NO氧化成NO2后,被电石渣吸收脱除;除尘方式为袋式除尘。
干法脱硫脱硝除尘一体化装置刚投入运行时,脱硫剂、脱硝剂用量大,运行成本高,处理后烟气指标不能稳定长期达标排放,脱硫剂旋转给料机给料量太大,不能连续给料减少下料量;吸收塔锥形段COA脱硝容易结壁,降低脱硫塔的有效反应空间,影响脱硫效果;入口烟道COA喷枪喷嘴材质为碳化硅易损坏;吸收塔出口温度高,NOx吸收效果差,电石渣耗量大;电石渣水分含量高,粒度大。
2 改造方案
(1)更换旋转给料机齿轮,减少下料量,稳定添加电石渣,保证二氧化指标稳定在10-35mg/Nm3 之间,降低了脱硫剂消耗。
(2)对原设计进行改造,更换原短喷枪为长喷枪,解决了结壁问题,不再因结壁问题而停运检修,保证了烟气脱硫系统长周期运行。
(3)入口烟道COA喷枪喷嘴材质原为碳化硅,易损坏,更换了2205双向钢材质,更耐腐蚀,为长周期运行奠定基础。
(4)针对电石渣水分含量高、粒度大问题,与脱硫剂供货方签订技术协议,要求对方增加过筛工艺,提供水分和粒度合格的电石渣。该措施降低了给料机的故障率,进一步解决了脱硫剂结块问题。
3 优化操作方案
3.1 做好炉内脱硝(LNB+SNCR)和干法脱硫脱硝的优化运行
3.1.1当锅炉煤质较好时,炉内燃烧器和水冷壁结焦情况不严重时,应首先加强炉内的LNB
(1)做好炉内低空气燃烧。通过降低主燃烧区的含氧量,抑制NOX的生成。(2)做好空气的分级燃烧。优化燃尽风与主燃烧区风量的配比。(3)做好燃料的分级燃烧。
3.1.2当锅炉煤质较差,炉内燃烧器和水冷壁结焦情况严重时,应加强炉内的SNCR操作
(1)控制好SNCR脱硝稀释水泵和氨水泵的流量调节,将入炉氨水浓度控制在10%左右。(2)根据炉内燃烧情况,选择合适的喷射层。(3)做好氨逃逸表的监控,严格控制氨逃逸,以免造成对后续设备的堵塞或腐蚀。
3.1.3 做好干法脱硫脱硝的运行
(1)控制好亚氯酸钠溶液的浓度在10%~15%。(2)做好电石渣和亚氯酸钠溶液的联合脱硝。(3)做好亚氯酸钠喷枪的日常检查维护,保证溶液的雾化效果,保证亚氯酸钠利用率。(4)根据吸收塔入口氮氧化物浓度,结合理论计算,控制亚氯酸钠的用量。(5)做好吸收塔COA和烟道超洁净COA的优化运行。
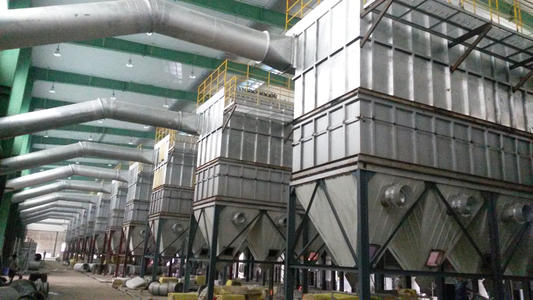
3.2 做好干法脱硫脱硝除尘的运行
(1)控制好净烟气工艺指标,力争控制SO2 浓度在10~35mg/Nm3。
(2)尽量提高吸收塔床层压降,通过增大循环灰流量,提高吸收塔内物料浓度,以提高循环物料的利用率。
(3)控制好吸收塔出口烟气温度,通过技术优化调整,将该温度由目前的95℃逐步降低到75~80℃之间,达到Ca(OH)2的*佳吸收温度。
(4)控制好电石渣来料质量,保证电石渣Ca(OH)2的含量、水分和细度。
4 改造和优化运行效果
4.1 减少了原除尘工艺中的问题
改造方案实施后,解决了脱硫剂给料机下料过大、COA脱硝喷嘴周围挂壁、喷嘴腐蚀、脱硝剂质量等问题,降低了故障停运率,确保了长周期运行,节能降耗,为烟气指标长期稳定达标排放奠定了基础。
4.2 降低了脱硫剂、脱硝剂消耗
2015年11月运行初期,电石渣和亚氯酸钠消耗量较大,经过2016 年优化运行后,消耗明显降低,月均消耗分别降低了37.1%、33%,达到设计消耗水平。
4.3 实现了较好的环境效益和社会效益
本脱硫脱硝除尘改造方案的实施,使烟囱排放的SO2、氮氧化物及烟尘减少,烟气出口指标稳定达到SO2 浓度<50mg/Nm3,NOX浓度<100mg/Nm3,含尘量<20mg/Nm3,满足现行环保排放标准。对大气环境质量、改善人民的生活质量和保证经济的可持续发展将起到显著的作用,实现环境效益和社会效益的双赢。
版权声明:本网注明来源为“乐发环保”的文字、图片内容,版权均属本站所有,如若转载,请注明本文出处:http://www.keketie.com 。同时本网转载内容仅为传播资讯,不代表本网观点。如涉及作品内容、版权和其它问题,请与本网站联系,我们将在及时删除内容。