当前,燃煤电厂*有效的脱硝技术是选择催化还原法(SCR),该技术具有效率高、选择性好、技术成熟等优点,广泛用于火电厂脱硝系统。本文系统分析了SCR脱硝过程中催化剂失活机理,并主要就对燃煤电厂失效脱硝催化剂的处理现状及前景进行分析和探讨
1、SCR脱硝反应概述
根据SCR催化剂和反应器的布置位置不同,SCR脱硝技术可以划分为3种工艺:高含尘工艺、低含尘工艺和尾部布置工艺。高含尘工艺的SCR催化剂和反应器布置在锅炉省煤器后空气预热器前(除尘器之前),该部分烟气温度在300~400℃左右,催化剂在此温度下有足够的活性,烟气不需加热即可获得较好NOx脱除效果。目前燃煤电厂SCR工艺主要采用高含尘工艺。
低含尘工艺的SCR催化剂和反应器布置在高温除尘器与空气预热器之间(除尘器后),该布置可防止烟气中飞灰对催化剂的污染及对反应器的磨损和堵塞,但是一般电除尘在300~400℃高温下难以正常运行,可靠性不高,一般不采用。尾部布置工艺的SCR催化剂和反应器布置在FGD(湿式尾气脱硫)系统之后,催化剂不受飞灰和三氧化硫等有害物质的影响。但由于烟气温度较低,一般要将烟气温度加热到催化剂所需活化温度,增加了运行成本。
2、催化剂的失活机理
燃煤电厂用脱硝催化剂在长期运行过程中会出现不断的失活。失活的主要原因包括:飞灰颗粒覆盖在催化剂的表面或造成催化剂孔道堵塞;飞灰中携带的碱金属、碱土金属、磷、砷和汞等导致的催化剂化学中毒;在高温和高速烟气的冲击下,催化剂发生热烧结和物理磨损与活性组分流失。尽管SCR催化剂的失活机理较为复杂且随着催化剂运行环境不同而不同,但通过研究各种不同失活机理,并找到相应的失活预防措施和催化剂的再生技术无疑对燃煤电厂脱硝尤为重要。
2.1表面覆盖与催化剂孔道堵塞
烟气中存在大量各种不同大小颗粒的飞灰,这些飞灰有的随着气流聚集在催化剂的表面,直接覆盖了催化剂的有效活性表面;有的飞灰颗粒搭桥形成大的颗粒造成催化剂的宏观孔堵塞;还有不少细微的飞灰颗粒可能进入催化剂的孔道中,导致孔道堵塞,致使NH3和NO无法扩散到催化剂内部孔道中发生反应。
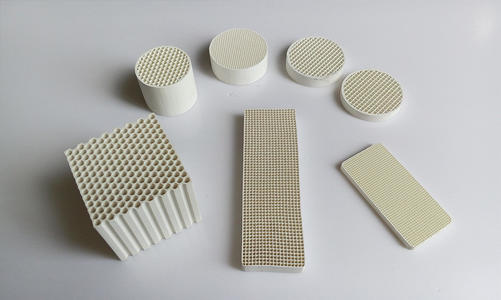
2.2催化剂活性组分流失与磨损
催化剂活性组分V2O5在高温下容易挥发,导致活性中心减少,引起催化剂反应性能下降。催化剂在使用过程中,遇到积灰严重的场合,通常用水来冲洗催化剂床层,以降低系统压降。然而钒的氧化物会溶解于水,进而导致部分活性组分的流失。催化剂磨损是烟气中飞灰与催化剂碰撞引起的,其磨损程度与烟气流速、飞灰含量、反应器流场分布和催化剂本身的强度等有关。催化剂磨损的主要部位是其迎灰面的端部。磨损对蜂窝式和波纹板式催化剂影响较大,严重时可观察到催化剂整体结构的坍塌,因此在催化剂制备过程中必需对其迎灰面端部进行硬化处理。板式催化剂的端部被磨损后,不锈钢基底暴露在迎灰面,可阻止烟气的的进一步磨损。
在高飞灰条件下,催化剂的内表面也会出现一定程度的磨损,引起活性组分的流失,导致催化剂活性降低。催化剂内表面的磨损程度与催化剂本身的制备方法有很大关系。通常一体成型的催化剂结构比采用表面涂覆制备的催化剂更有利于提高催化剂的抗磨性能。
2.3催化剂高温热烧结
受催化剂活性温度窗口限制,目前工业上使用的钒钛基催化剂需要在较高温度下运行。在脱硝反应器入口,烟气的温度一般都超过400℃,当锅炉运转出现波动时,脱硝反应器内的温度极有可能大幅上升。因此,烧结是大多数电厂SCR脱硝催化剂失活的重要原因之一。催化剂的烧结是一个不可逆的过程,它导致活性成分V2O5的颗粒长大,载体TiO2的孔道数量和比表面变小,直接减少了催化反应活性位的数量。
3、催化剂处理方式
脱硝催化剂是SCR技术的核心部件,使用约三年后进行更换,根据脱硝催化剂的失活原因从而对失效催化剂进行再生处理或回收。
3.1失效催化剂的再生处理
这是将失活的催化剂通过一系列物理或化学程序,恢复其部分活性,使其能够再次达到所需性能的一种方式。催化剂再生需要在现场采用专用工具进行该一系列的操作,通常的程序包括应用严格的物理方法去除沉淀粉尘,再采用化学解决方案对失活催化剂进行再生,可将失活催化剂的化学活性恢复。再生后催化剂的脱硝活性可以恢复新催化剂的90%;磨损强度和机械强度分别可达新催化剂的87.95%和88.90%;SO2氧化率等性能指标可以与新催化剂接近,再生后催化剂的SO2/SO3转化率小于1%,再生后催化剂的机械寿命应大于5年,化学寿命应大于1.6万小时。在实际的处理过程中,通常需要先对失效催化剂的失活原因进行取样分析,再制定具体的再生程序。因此,这些工作需要具有专利技术的国外专业公司进行操作,才能在不损伤催化剂的前提下恢复一定的活性。而再生的效果亦取决于催化剂的失活原因,物理原因例如堵塞,再生的效果要好一些,化学原因则需要看催化剂的变质是否属于不可逆转的机理,以及可恢复活性的程度。催化剂再生的成本则取决于再生程序的复杂程度,复杂的再生程序成本有时会高于替换同体积的全新催化剂,因此在采用该种方式处理实效催化剂时,需要综合考虑经济与远期运行的效果。
3.2失效催化剂的回收处理
失效催化剂的常用回收方法可分为间接回收法和直接回收法。其中直接回收法又可分为分离法和不分离法,间接回收法可分为干法、湿法和干湿结合法。受到各种因素的制约,以及回收效益的影响,一般失效催化剂的回收方法多采用间接回收法。间接回收法主要分为:
(1)干法回收工艺
干法回收是用固体碱与废催化剂混合,在空气中灼烧熔融,使其中的V2O5转变为水溶性的钒酸盐。加水溶解K3VO4,分离TiO2和K3VO4,将溶液煮沸,钒酸盐水解析出V2O5。干法提钒一般燃料及碱消耗量大,回收钒成本高。同时,由于废催化剂中SiO2,Al2O3等杂质元素焙烧时,钒转化为不溶于水的含钒硅酸盐,钒氧化物从水浸出率降低,详细工艺需进一步研究。
(2)湿法回收工艺
催化剂经使用后,其中的钒主要以V2O5和VOSO4形式存在,后者所占比例有时可达40%~60%。催化剂中低价含钒盐易溶于酸而难溶于碱,而V2O5易溶于碱难溶于酸,因而可用酸液或碱液浸取,一些研究大都用酸浸取。湿法回收催化剂成分的工艺为一般可分为:沉淀法、萃取法和离子交换法等物理化学方法。沉淀法主要是在一些介质中钒酸、钨酸和钼酸的溶解度不同,可以通过温度的升高,来实现钒钨钼的分离;萃取法主要通过萃取剂实现钒钨钼的可溶性盐溶液的分离;离子交换法是通过钨钼酸根在离子交换树脂吸附的差异,从而对钨钼进行分离。废弃脱硝催化剂再生与回收技术是具有创新性和巨大的市场应用前景的技术,该项技术也成为各催化剂生产厂的研究热点。
版权声明:本网注明来源为“乐发环保”的文字、图片内容,版权均属本站所有,如若转载,请注明本文出处:http://www.keketie.com 。同时本网转载内容仅为传播资讯,不代表本网观点。如涉及作品内容、版权和其它问题,请与本网站联系,我们将在及时删除内容。